Lubricants in the Global Plastic Processing Market Trends and Forecast
Lucintel finds that the future of the lubricants in the global plastic processing market looks promising with opportunities in the construction, packaging, consumer goods, and automotive industries. The lubricant in the plastic processing market is expected to reach an estimated $71 billion by 2030 with a CAGR of 5% from 2023 to 2030. The major drivers for this market are growing demand for plastics in various end use markets, including construction, packaging, consumer goods, and automotive and increased demand for lubricants to reduce frictional forces and to improve processing & productivity of plastics manufacturing.
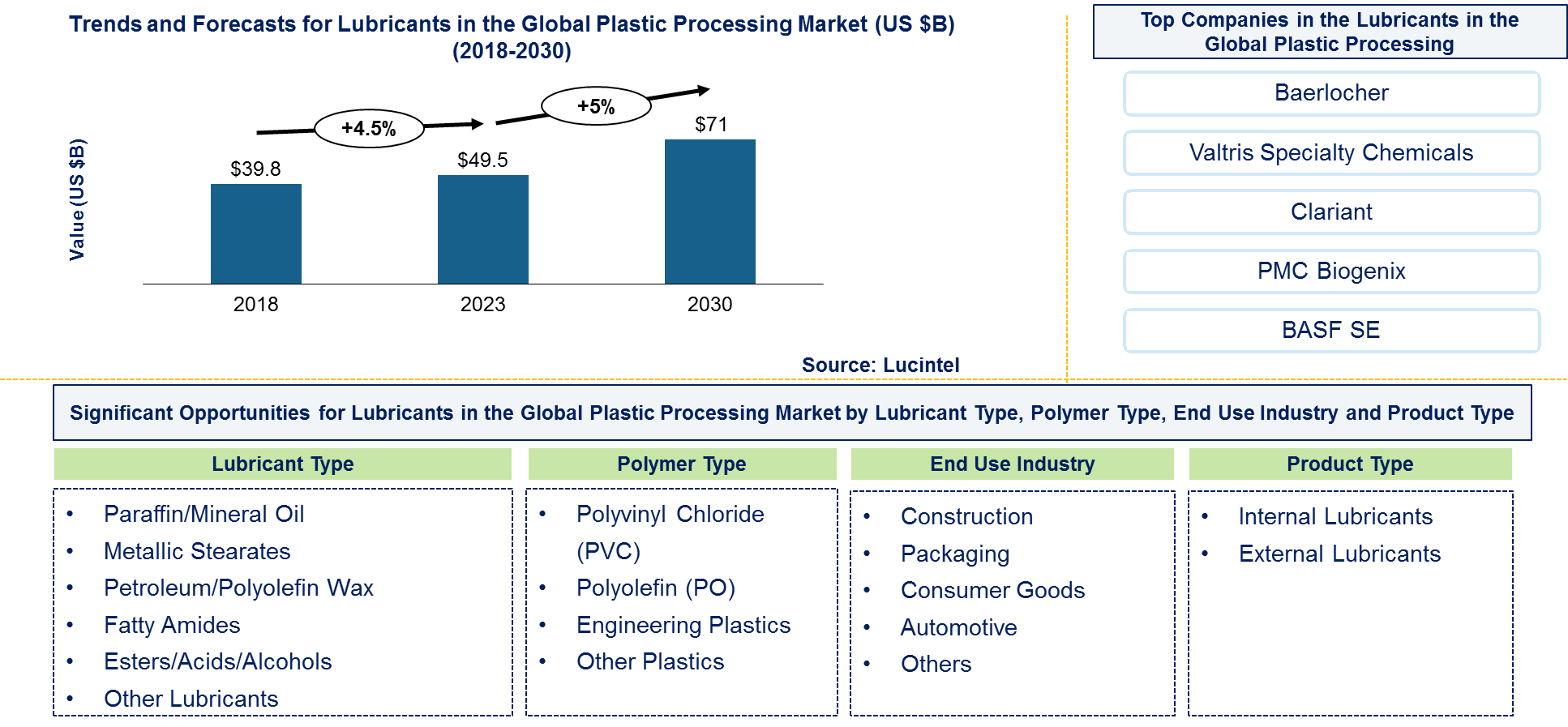
Lubricants for plastic processing are specialized additives used to improve the processing of polymers during manufacturing. These lubricants enhance flow characteristics, reduce friction and wear, and prevent material degradation, leading to better product quality and efficiency in production. Common types of lubricants include internal lubricants, which are mixed with the polymer to reduce viscosity, and external lubricants, which are applied to processing equipment to minimize friction. The primary raw materials for these lubricants often include fatty acids, fatty alcohols, esters, and waxes. Additionally, synthetic lubricants and polymer-based lubricants may also be employed to achieve specific performance characteristics tailored to different plastic processing techniques such as extrusion, injection molding, and blow molding. The choice of lubricant depends on the type of plastic being processed and the specific requirements of the manufacturing process.
• Lucintel forecasts that metallic stearates will remain the largest market due to their wide usage as internal and external lubricants in PVC and other plastic processing industries. Lucintel predicts that paraffin/mineral oil will witness the fastest growth during the forecast period due to the increasing consumption of paraffin as an external lubricant and secondary plasticizer in PVC processing.
• Within lubricants in the plastic processing market, PVC will remain the largest polymer by value and volume due to the increasing demand for PVC in various applications such as, pipes, packaging, wire & cable, flooring, roofing, building materials, consumer goods, healthcare, and automotive parts.
• Asia Pacific is expected to remain the largest market by value and volume and witness the highest growth over the forecast period due to the growing demand for plastics in construction, packaging, and automotive industries.
Country wise Outlook for Lubricants in the Global Plastic Processing Market
Major players in the market are expanding their operations and forming strategic partnerships to strengthen their positions. Below image highlights recent developments by major lubricants in the global plastic processing producers in key regions: the USA, Brazil, Germany, China, India, and Japan.
Emerging Trends in Lubricants in the Global Plastic Processing Market
The lubricants in the global plastic processing market's size has been expanding rapidly, driven by the increasing adoption of lubricants in plastic processing in various industries. The market size is influenced by factors such as of sustainable bio-based lubricants, advancement in formulation technology of lubricants, and development of specialized lubricants for various applications. The market size is estimated to continue its upward trajectory as industries across the globe seek to improve performance, efficiency, and sustainability.
Emerging trends in lubricants in the global plastic processing market are shaping its future applications and market dynamics:
• Sustainable Bio-based Lubricants: There is a developing need for eco-friendly lubricants. Producers are turning to bio-based and biodegradable lubricants produced from renewable sources more and more. This change helps in reducing the environmental impact and well-aligned with global sustainability objectives.
• Specialized Lubricants for Various Applications: The market has experienced rise in coming up with specialized lubricants which are specific to different types of plastics and methods of processing. This customization optimizes performance in injection molding, extrusion or blow molding applications.
• Emphasis on Non-Toxicity and Safety Concerns over Lubrication: Since health & safety regulations become tougher there is a rising focus on producing non-toxic lubricants that these products ensures safety of workers as well as compliance with regulatory standards particularly for food packaging and medical applications.
• Digitization plus Intelligent Lubrication Solutions: Digitalizing trend within the management of lubricating system is increasing day by day through which real time monitoring optimization towards use of lubricant via smart systems containing sensors analytics therefore assisting enhancing efficiencies minimization wastages.
• Emerging Markets And Increased Demand: Growing industrialization in EMs (Emerging markets) has resulted into increased demand for plastic-processing-lubricants during these investments into manufacturing capacities are being made; their effectiveness to enhance productivity qualify calls for effective lubes.
A total of 145 figures / charts and 120 tables are provided in this 243 -page report to help in your business decisions. Sample figures with some insights are shown below.
Recent Developments in Lubricants in the Global Plastic Processing Market
Recent developments in lubricants in the global plastic processing market which highlights ongoing innovations and advancements across different sectors:
• Sustainability Initiatives: In recent times, the lubricant industry has seen a swing towards sustainable alternatives such as bio based and biodegradable products. These eco-friendly lubricants aim at minimizing damage to the environment and aligning with worldwide objectives on sustainability.
• Advanced Formulations: Advancements in lubricant formulations have led to high-performance products designed for specific processing methods. Such developments have resulted in advanced lubricating oils that improve machine efficiency, reduce friction and enhance the quality of plastic materials.
• Regulatory Compliance: The latest trends indicate that there is greater emphasis on environmental and health compliance. They are developing non-hazardous but efficient industrial oils to conform them to legal requirements especially food industries and medical sectors require non-toxic certified grades.
• Integration of Digital Technologies: Smart lubrication solutions are becoming more popular every day. Owing to this, digital technologies like IoT internet of things) and data analytics are being used in lube management systems for better usage optimization, performance monitoring, and less waste creation.
• Customized Lubricant Solutions: There is a growing demand for tailored lubricants which are intended for particular plastics or processing technologies. Thus, they develop tailor-made items that can enhance operations for different applications ranging from injection molding up extrusion processes among others.
• Emerging Market Growth: The rapid industrialization in emerging economies creates a need for high performing lubes for plastics industry operations. Accordingly, market expansion there necessitates solutions that will help raise productivity as well as product excellence.
• Focus on Non-toxic Solutions: Increased concern over safety is driving the trend towards environmentally friendly lubricants free from hazardous substances A crucial step towards ensuring workers’ safety while adhering to regulatory frameworks involves shifting from toxic alternatives into harmless ones.
Strategic Growth Opportunities for Lubricants in the Global Plastic Processing Market
The lubricants market within the plastic processing sector is poised for significant growth, driven by technological advancements, evolving industry needs, and sustainability goals. Following are the strategic growth opportunities in the lubricants in the global plastic processing market:
• Sustainability and Environmentally Friendly Solutions: The growing trend towards bio based and biodegradable lubricants is an opportunity to develop innovative formulations that meet sustainability requirements in the face of increasing environmental regulations and consumer demand for sustainable products.
• Customization for Specific Applications: Specialized lubricants that are tailored to individual processes for example injection molding, extrusion and blow molding have a large potential for growth. Performance and efficiency can be improved through custom formulation hence meeting the different needs of customers.
• Integration with Advanced Technologies: Integrating lubricants into new technological trends such as IoT, smart sensors among others can help optimize the way they are used within an organization. Efficiency might be increased, wastage reduced as well as providing real time information for better control in operations.
• Expansion into Emerging Markets: Lubricant manufacturers stand to gain substantially from developing markets that experience rapid industrialization. Through presence creation in these markets and offering differentiated solutions, new customer base will be attracted and the extent of their market coverage will expand accordingly.
• Focus on Non-Toxic and Safe Lubricants: Growing awareness about health & safety standards provides a chance to create non-toxic lubricants. This will attract companies in sensitive sectors like food packaging or healthcare by making formulations which adhere to stringent safety standards.
Lubricants in the Global Plastic Processing Market Driver and Challenges
Lubricant in the global plastic processing has a very important role in many industries including construction, packaging, consumer goods, and automotive industries The changing market dynamics are being driven by the growing demand for high-performance plastics and increasing sustainability initiatives. However, challenges like high initial cost and technological limitations to sustain growth and innovation in lubricants in the global plastic processing market. The factors responsible for driving the lubricants in the global plastic processing market include:
• Rising Demand for High-Performance Plastics: The requirement for high-quality plastic products by various industries such as automotive, packaging and consumer goods is increasing the need for effective lubricants that improve processing efficiency and product performance.
• Sustainability Initiatives: There is a great deal of movement in relation to sustainability. This has resulted in development of eco-friendly lubricants. With companies seeking to cut their environmental footprint, there is an upsurge in bio-based and biodegradable lubricants.
• Technological Advancements: Improved lubricant formulations and processing technologies are changing how effective the lubricants are. Well improved flow characteristics as well as reduced friction are among its advanced formulas that are increasingly demanded.
• Rising Regulatory Standards: Non-toxic compliant lubes have been adopted by manufacturers as a result of strict health and safety regulations. To this end, market growth is supported since companies require non-threatening ways of handling sensitive applications like food packaging or medical devices.
• Expansion of Plastic Processing Industries: Growth of plastic processing industries in emerging markets creates room for new entrants who supply them with oils. It becomes imperative to look out for efficient and targeted oils as these sectors grow bigger.
Challenges facing the lubricants in the global plastic processing market are:
• High Initial Costs: Some manufacturers may be put off by the prices associated with premium quality oiling agents hence preventing them from going forward with advanced solutions. The market still grapples with striking a balance between price and performance.
• Technological Limitations: Thermal stability, compatibility with different plastics, long-term performance are some limitations current lube techs may have. For any market growth, it is important to overcome all those technical hurdles.
• Regulatory Compliance Issues: Entering complex regulatory settings can be burdensome. Compliance with changing rules can lead to increased costs or even issues surrounding operations on the part of manufacturers.
• Competition from Alternative Solutions: The market therefore faces competition from alternate process aids like processing additives and surfactants which could equally provide similar benefits without the necessity for oils.
• Supply Chain Disruptions: The geopolitical issues, economic fluctuations and supply chain disruptions have an effect on raw material availability that is used to make lubricants hence affecting the general market stability.
Performance, sustainability as well as regulatory compliance are driving the plastic processing lubricant market. However, there are hurdles such as high costs and regulatory complexities that must be faced to ensure continued growth and innovation. This evolving market can be better positioned for success by understanding these dynamics.
Lubricants in the Global Plastic Processing Suppliers and their Market Shares
In this globally competitive market, several key players such as Baerlocher, Valtris Specialty Chemicals, Clariant, PMC Biogenix, BASF SE, Peter Greven, Faci, FERRO-PLAST, and Exxon Mobil etc. dominate the market and contribute to industry’s growth and innovation. These players capture maximum market share. To know the current market share of each of major players, contact us by email at helpdesk@lucintel.com.
Companies in the market compete on the basis of product quality offered. Major players in this market focus on expanding their manufacturing facilities, R&D investments, infrastructural development, and leverage integration opportunities across the value chain. With these strategies, lubricants in the global plastic processing companies cater to increasing demand, ensure competitive effectiveness, develop innovative products & technologies, reduce production costs, and expand their customer base. Some of the lubricants in the global plastic processing companies profiled in this report include:
• Baerlocher
• Valtris Specialty Chemicals
• Clariant
• PMC Biogenix
• BASF SE
• Peter Greven
• Faci
• FERRO-PLAST
• Exxon Mobil
These companies have established themselves as leaders in lubricants in the global plastic processing industry, with extensive product portfolios, global presence, and strong research and development capabilities. They continually strive to enhance their market positions through strategic partnerships, mergers and acquisitions, and product innovations.
The market share dynamics within the in lubricants in the global plastic processing market are evolving, with the entry of new players and the emergence of in lubricants in the global plastic processing technologies. Additionally, collaborations between component suppliers, manufacturers, and end-users are fostering technological advancements and expanding market opportunities.
0
Lubricants in the Global Plastic Processing Market by Segment
Major segments of lubricants in the global plastic processing that are experiencing growth include construction, packaging, consumer goods, automotive, and others. As industries adopt eco-friendly and specialized lubricants, growth opportunities are expanding, particularly in emerging markets. Technological advancements and stricter regulatory standards are further shaping the landscape, encouraging innovation. Additionally, the integration of smart technologies for lubricant management is poised to enhance efficiency.
This lubricants in the global plastic processing market report provides a comprehensive analysis of the market's current trends, growth drivers, challenges, and future prospects in all major segments like above. It covers various segments, including lubricant type, polymer type, product type, and end use industry. The report offers insights into regional dynamics, highlighting the major markets for lubricant in the global plastic processing and their growth potentials. The study includes trends and forecast for the lubricant in the global plastic processing market by lubricant type, polymer type, end use industry, product type, and region as follows:
Lubricants in the Plastic Processing Market by Lubricant Type [Volume (Kilotons) and $M Analysis for 2018 – 2030]:
• Paraffin/Mineral Oil
• Metallic Stearates
• Petroleum/Polyolefin Wax
• Fatty Amides
• Esters/Acids/Alcohols
• Other Lubricants
Lubricants in the Plastic Processing Market by Polymer Type [Volume (Kilotons) and $M Analysis for 2018 – 2030]:
• Polyvinyl Chloride (PVC)
• Polyolefin (PO)
• Engineering Plastics
• Other Plastics
Lubricants in the Plastic Processing Market by End Use Industry [Volume (Kilotons) and $M Analysis for 2018 – 2030]:
• Construction
• Packaging
• Consumer Goods
• Automotive
• Others
Lubricants in the Plastic Processing Market by Product Type [Volume (Kilotons) and $M Analysis for 2018 – 2030]:
• Internal Lubricants
• External Lubricants
Lubricants in the Plastic Processing Market by Region [Volume (Kilotons) and $M Analysis for 2018 – 2030]:
• North America
o US
o Canada
o Mexico
• Europe
o Eastern Europe
o Western Europe
• Asia Pacific
o China
o India
o South Korea
o Japan
• The Rest of the World
Features of Lubricants in the Global Plastic Processing Market
Market size estimates: Lubricants in the plastic processing market size estimation in terms of value ($M) and volume (Kilotons) shipment.
Trend and forecast analysis: Market trend (2018-2023) and forecast (2024-2030) by lubricant type, polymer type, product type, and end use industry
Segmentation analysis: Lubricants in the plastic processing market size by lubricant type, polymer type, product type, end use industry in terms of value and volume shipment.
Regional analysis: Lubricants in the plastic processing market breakdown by North America, Europe, Asia Pacific, and the Rest of the World.
Growth opportunities: Analysis on growth opportunities in different segments and regions of lubricants in the plastic processing market.
Strategic analysis: This includes M&A, new product development, and competitive landscape of lubricants in the plastic processing market.
Analysis of competitive intensity of the industry based on Porter’s Five Forces model.
This report answers following 11 key questions
Q.1 What are some of the most promising potential, high-growth opportunities for lubricants in the plastic market by lubricant type (paraffin/mineral oil, metallic stearates, petroleum/polyolefin wax, fatty amides, esters/acids/alcohols, and others), polymer type (polyvinyl chloride [PVC], polyolefin [PO], engineering plastics, and other plastics), product type (internal lubricants and external lubricants), end use industry (construction, packaging, consumer goods, automotive, others), and region (North America, Europe, Asia Pacific, and the Rest of the World)?
Q.2 Which segments will grow at a faster pace and why?
Q.3 Which regions will grow at a faster pace and why?
Q.4 What are the key factors affecting market dynamics? What are the drivers and challenges of lubricants in the plastic processing market?
Q.5 What are the business risks and threats to lubricants in the plastic processing market?
Q.6 What are emerging trends of lubricants in the plastic processing market and the reasons behind them?
Q.7 What are some changing demands of customers of lubricants in the plastic processing market?
Q.8 What are the new developments of lubricants in the plastic processing market? Which companies are leading these developments?
Q.9 Who are the major players of lubricants in the plastic processing market? What strategic initiatives are being implemented by key players for business growth?
Q.10 What are some of the competitive products and processes of lubricants in the plastic processing area and how big of a threat do they pose for loss of market share via material or product substitution?
Q.11 What M & A activities have taken place in the last 7 years of lubricants in the plastic processing market?