Composites in the Global Oil and Gas Industry Trends and Forecast
Lucintel finds that the future of the composites products such as pipes, tanks, pultruded products, and frac plugs and frac balls in the oil and gas industry looks promising with opportunities pipes, tanks, pultruded products, frac plugs and frac balls end uses. The global composite tooling material market is expected to reach an estimated $4 million by 2030 with a CAGR of 13% from 2023 to 2030. The major drivers of growth for this market are increasing oil and gas drilling and exploration activities in future.
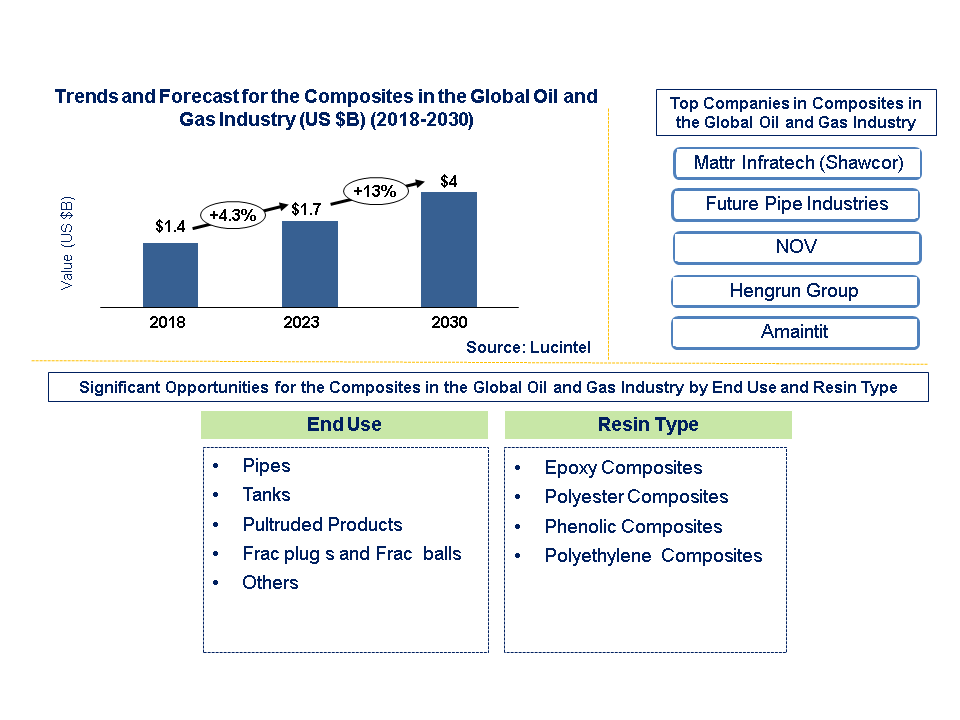
The composites used in the oil and gas market are made from reinforcing fibers like glass, carbon or aramid held together by matrix resins such as epoxy, vinyl ester or polyester. These materials are selected because of their ability to withstand harsh environmental conditions as well as their strength and durability. Additives and fillers can also be present in order to improve properties like impact resistance, UV stability and chemical resistance. Consequently, they combine mechanical performance and longevity necessary for the demanding applications within the oil & gas industry.
Usually, composites in the oil and gas market cost more than conventional materials such as steel or aluminum because of expensive high-performance fibers and resins. However, their excellent resistance to corrosion, chemicals or extreme temperatures can justify this higher cost over time through reduced maintenance and extended service life. Despite being competitive with other advanced composites designed for aerospace or automotive purposes, pricing is specific depending on material types as well as performance requirements.
• Lucintel forecasts pipe is expected to remain as the largest market by value and volume consumption and it is also expected to experience the highest growth in the forecast period due to increases in oil and gas production and exploration activity on both onshore and offshore production sites have increased the demand for pipes are the major driving forces that spur the growth for this segment over the forecast period.
• Epoxy composites will remain the largest segment over the forecast period supported by its high performance characteristics such as low shrinkage, excellent adhesion, effective electrical insulation, high chemical, and solvent resistance properties. Polyethylene composites is expected to witness highest growth over the forecast period.
• North America will remain the largest market over the forecast period due to growth in natural gas infrastructure projects, and awareness on the advantages of composite materials for oil and gas over traditional material. ROW is expected to witness highest growth over the forecast period.
Country wise Outlook for the Composites in the Oil and Gas Market
Emerging Trends in the Composites in the Oil and Gas Market
Emerging trends in the composites in the oil and gas market shaping its future applications and market dynamics:
• Increasing Enhanced Durability and Performance: The development of high-performance resin systems, such as epoxy and vinyl ester formulations, is increasing the durability and chemical resistance of composites. It enables composites to better survive in harsh environments and endure chemicals that are aggressive found in oil and gas operations.
• Rising Demand for Lightweight and High Strength Materials: Their light weight property makes them serve as a good component to reinforce carbon fiber composites which have high strength. This trend supports more efficient and cost-effective designs for equipment and infrastructure while reducing structural weight or maintaining or improving performance.
• Corrosion and Impact Resistance: The new anti-corrosion coatings are prolonging the service life of composite materials used in corrosive environments, such as offshore platforms, pipelines etc. These coatings guard against degradation that arises from saltwater among others.
• Adoption of Advanced Manufacturing Techniques: The 3D printing adoption alongside advanced automated manufacturing processes has enabled fabrication of complex composite structures with shorter lead times and higher accuracy. Rapid prototyping is possible using these technologies thus making it affordable to produce customized components.
• Utilizing Smart Technologies: Embedded Sensors more often than not, incorporation of integrated sensors within composites helps capture data in real time. Structural safety information is obtained online through predictive maintenance techniques for ensuring operational integrity with less downtime leading to improved safety standards.
These trends indicate a shift towards more sustainable, innovative, and technologically advanced solutions for composites in the oil and gas industry to meet evolving consumer and regulatory demands globally.
A total of 98 figures / charts and 62 tables are provided in this 194-page report to help in your business decisions. A sample figure with insights is shown below.
Recent Developments in the Composites in the Oil and Gas Market
Recent developments in composites in the oil and gas Market which highlights ongoing innovations and advancements across different sectors
• Increasing Use in Offshore Applications: Composites are being used increasingly in offshore oil and gas activities for various purposes such as subsea structures, risers, pipelines, and platform components. The composites with their lightweight nature and resistance to corrosion make them attractive for use in offshore installations where there is need for weight reduction as well as protection against harsh marine environments.
• Focus on Cost Reduction and Efficiency: There is mounting interest in composites as a low cost alternative to conventional materials such as steel due to the ongoing pressure on reduced costs and increased operational efficiency within the oil & gas industry. Composite materials have benefits like lower installation/maintenance expenses, longer life, enhanced asset performance; all these contribute towards savings that operators can enjoy generally.
• Integration of Composite Technologies: Collaborations, partnerships or technology transfer agreements with composite material suppliers/manufacturers are some ways through which companies in oil & gas sector are integrating composite technologies into their operations. Such collaborations enable development of tailor-made composite solutions designed to address specific challenges facing this industry.
• Emphasis on Safety and Environmental Compliance: When it comes to the adoption of composite materials by the oil and gas sector safety alongside environmental concerns play a critical role. Composites offer advantages such as non-conductivity, fire resistance, and resistance to chemical corrosion making them suitable for applications where safety standards must be maintained within environmentally sensitive areas.
Strategic Growth Opportunities for Composites in the Oil and Gas Market
The advancements in manufacturing technologies, material performance and sustainability fuel strategic growth prospects of composites in the oil and gas market. Innovations in this sector have led to increased lifespan of products, resistance to rusting and efficiency thereby making it possible for industries to effectively respond to changes as they take place. Some key strategic growth opportunities for this market include:
Technological Developments in Materials:
• High Performance Resinous Systems: Development of new kinds of resin systems like epoxy and Vinyl ester resins enhances durability and chemical resistance of composites. This breakthrough is tailored to the harsh environmental conditions typical at oil and gas fields hence prolongs their life span while minimizing maintenance costs.
Improved Manufacturing Processes:
• 3D Printing and Automation: The adoption of additive manufacturing techniques through 3D printing and automated production has enabled the manufacture of more accurately complex composite structures with better efficiency. Shorter lead times, lower costing, as well as quick prototyping are possible due to these technologies for tailor-made solutions in different user industries.
Corrosion Resistance and Wear Protection:
• Advanced Coatings: Innovations in anti-corrosive coatings and treatments can enhance the corrosive resistance of composites to salty water, chemicals etc. thus encountered within offshore or subsea environments. More durable equipment and infrastructure can therefore be developed using this approach.
Integration with Smart Technologies:
• Embedded Sensors: Incorporation of sensors into composites allows for real-time monitoring for operational safety and efficiency. Predictive maintenance, structural health monitoring, as well as informed decision-making are some benefits provided by intelligent materials based on real time performance analytics.
Collaborative Industry Partnerships:
• Joint Ventures and R&D: Strategic collaboration with industry giants and research institutions can promote creativity and encourage the emergence of advanced composite materials. Cooperative research and development (R&D) programs may yield new discoveries in material functionality and application possibilities.
Regulatory Compliance and Certification:
• Meeting Industry Standards: Composite materials must meet strict industry standards as well as comply with regulatory requirements. Certifications for performance and safety can bolster credibility within the oil and gas industry, paving the way for additional projects or applications.
Composites in the Oil and Gas Market Drivers and Challenges
The advanced materials are needed in the oil and gas sector to cater for the harsh conditions of the industry. These composites have several advantages such as enhanced toughness, weight savings, and resistance to corrosion. The growth will be supported by technological advancements that have been made on resins and manufacturing processes. However, high costs of production, difficult recycling procedures, competition from established materials are obstacles encountered in this market segment. For composites to achieve their maximum potential they must reconcile these influencers with challenges that hinder progress in order to meet industry standards at competitive costs while effectively conserving environment resources.
The factors responsible for driving the composites in the oil and gas market include:
1. Improved Performance and Durability: Composites have higher strength-to-weight ratios, resistance to corrosion and are durable enough to withstand the tough environments in the oil and gas industry. Modern polymer systems such as epoxies and vinyl esters can be applied to withstand harsh temperatures and aggressive chemicals thereby increasing service life of infrastructure.
2. Benefits of Weight Reduction: The small weight associated with composites allows for reduced transportation costs, minimizes installation expenses, and enhances efficiency during operations. Reduced overall weight such as in pipes or offshore structures made from composites is crucial in handling difficult climatic conditions.
3. Advanced Manufacturing Techniques: There are currently new manufacturing technologies like 3D printing and automated fiber placement that enable production of complex composite parts with high precision. This will lead to faster prototyping and customization thus supporting leaner more productive manufacturing processes.
4. Sustainability versus Environmental Concerns: The greater focus on sustainability has given rise to recyclable composites and other eco-friendly materials. They satisfy green objectives stated by international regulators, assist sectors in lessening their carbon footprints through various circular economy practices.
Challenges in the Composites in the Oil and Gas Market:
1. High Production Costs: The price of fabricating composite materials including high end fibers and resins is more expensive in comparison with traditional materials like aluminum and steel. These increased expenses may affect the economic viability of using composites, particularly in cost conscious applications.
2. Recycling and End-of-Life Management: Crackling down on wastes involving composites is problematic since it becomes hard to separate the fibers from the matrix material. Consequently, this complicates waste management and disposal, leading to environmental as well as logistical problems for end-of-life management of composite components.
3. Competition from Traditional Materials: Composites face competition from conventional materials such as steel and aluminum that might have lower initial costs and already established performance characteristics. As a result, this can influence market adoption and pricing strategies for composites.
The challenges faced by composites in the oil and gas market can be such as high cost and difficulty in recycling, material science and manufacturing technologies are undergoing continuous innovations which are so important. The development of smart composites and sustainable practices creates room for potential solutions to be applied towards changing the market while at the same time effectively solving issues of performance and environmental impact.
Composites in the Oil and Gas Suppliers and Their Market Shares
In this globally competitive market, several key players such as, Mattr Infratech (Shawcor), NOV, Future Pipe Industries, Hengrun Group, Strongwell, etc. dominate the market and contribute to industry’s growth and innovation. These players capture maximum market share. To know the current market share of each of major players, contact us.
Companies in the market compete on the basis of product quality offered. Major players in this market focus on expanding their manufacturing facilities, R&D investments, infrastructural development, and leverage integration opportunities across the value chain. With these strategies composites in the oil and gas companies cater increasing demand, ensure competitive effectiveness, develop innovative products & technologies, reduce production costs, and expand their customer base. Some of the composites in the oil and gas companies profiled in this report include.
• Mattr Infratech (Shawcor)
• Future Pipe Industries
• National Oilwell Varco (NOV)
• Hengrun Group
• Strongwell
• Amiantit
• Baker Hughes
These companies have established themselves as leaders in the composites in the oil and gas industry with extensive product portfolios, global presence, and strong research and development capabilities. They continually strive to enhance their market positions through strategic partnerships, mergers and acquisitions, and product innovations.
The market share dynamics within the composites in the oil and gas market are evolving, with the entry of new players and the emergence of innovative technologies. Additionally, collaborations between material suppliers, manufacturers, and end-users are fostering technological advancements and expanding market opportunities.
Composites in the Oil and Gas Market by Segment
The composites segment of the petroleum industry has seen a dramatic surge in pipeline growth because of their ability to withstand corrosion and harsh environments. The use of tanks has increased because they tolerate corrosive substances and retain their structural integrity too. Pultruded products are also growing, providing light and high-strength solutions for different structural applications such as support beams, frames etc.
The composites in the oil and gas market report provides a comprehensive analysis of the marketÄX%$%Xs current trends, growth drivers, challenges, and future prospects in all major segments like above. It covers various segments, include end use and resin type. The report offers insights into regional dynamics, highlighting the major markets for global balsa core material market and their growth potentials. The study includes trends and forecast for the composites in oil and gas market by end use, resin type and region as follows:
Composites in the Oil and Gas Industry by End Use [Value ($M) and Volume (M lbs) Analysis for 2018 – 2030]:
• Pipes
• Tanks
• Pultruded Products
• Frac Plugs and Frac Balls
• Others
Composites in the Oil and Gas Industry by Resin Type [Value ($M) and Volume (M lbs) Analysis for 2018 – 2030]
• Epoxy Composites
• Polyester Composites
• Phenolic Composites
• Polyethylene Composites
Composites in the Oil and Gas Industry by Region [Value ($M) and Volume (M lbs) Analysis for 2018 – 2030]:
• North America
• Europe
• Asia Pacific
• Rest Of the World
Features of Composites in the Global Oil and Gas Industry
• Market Size Estimates: Composites in the oil and gas industry market size estimation in terms of value ($M) and Volume (M lbs)
• Trend and Forecast Analysis: Market trends (2017-2022) and forecast (2023-2028) by various segments and regions.
• Segmentation Analysis: Market size by end use, resin type, and region.
• Regional Analysis: Composites in the oil and gas industry breakdown by North America, Europe, and Asia Pacific & the Rest of the World.
• Growth Opportunities: Analysis of growth opportunities in different end use, resin type, and regions for composites in the oil and gas industry.
• Strategic Analysis: This includes M&A, new product development, and competitive landscape for the composites in the oil and gas industry.
• Analysis of competitive intensity of the industry based on Porter’s Five Forces model.
If you are looking to expand your business in composites in the oil and gas market or adjacent markets, then contact us. We have done hundreds of strategic consulting projects in market entry, opportunity screening, due diligence, supply chain analysis, M & A, and more.
FAQ
Q1. What is the composite in the oil and gas industry size?
Answer: The composites in the global oil and gas industry is expected to reach an estimated to $861 million by 2030.
Q2. What is the growth forecast for composites in the oil and gas industry?
Answer: The composite in the global oil and gas industry is expected to grow at a CAGR of 6% from 2023 to 2030.
Q3. What are the major drivers influencing the growth of the composites in the oil and gas industry?
Answer: The major drivers of growth for this market are increasing oil and gas drilling and exploration activities in future.
Q4. What are the major applications or end use industries composites in the oil and gas?
Answer: Pipes and tanks are the major end uses for composites in the global oil and gas industry.
Q5. What are the emerging trends of composites in the oil and gas industry?
Answer: Emerging trends, which have a direct impact on the dynamics of the industry, are the emergence of introduction of carbon fiber for composites application in the oil and gas industry, on-site construction of FRP pipes to any length and diameter, and increasing demand for high temperature and pressure RTPs.
Q6. Who are the composites in the oil and gas companies?
Answer: Some of the key composites in the global oil and gas companies are as follows:
• Mattr Infratech
• Future Pipe Industries
• National Oilwell Varco (NOV)
• Hengrun Group
• Strongwell
• Amiantit
• Baker Hughes
Q7.Which composite in oil and gas resin type segment will be the largest in future?
Answer: Lucintel forecasts that epoxy composite resin type composites in the global oil and gas will remain the largest segment.
Q8: In composite in oil and gas, which region is expected to be the largest in next 7 years?
Answer: North America is expected to remain the largest region and witness the highest growth over next 7 years.
Q9. Do we receive customization in this report?
Answer: Yes, Lucintel provides 10% Customization Without any Additional Cost.
This report answers following 11 key questions
Q.1 What are some of the most promising potential, high growth opportunities for composites in the oil and gas industry by end use (pipes, tanks, pultruded products, frac plugs and frac balls, and others), resin type (epoxy composites, polyester composites, phenolic composites, and polyethylene composites), and region (North America, Europe, and Asia Pacific & Rest of the World)?
Q. 2 Which segments will grow at a faster pace and why?
Q.3 Which regions will grow at a faster pace and why?
Q.4 What are the key factors affecting market dynamics? What are the drivers and challenges of the market?
Q.5 What are the business risks and threats to the market?
Q.6 What are the emerging trends in this market and the reasons behind them?
Q.7 What are the changing demands of customers in the market?
Q.8 What are the new developments in the market? Which companies are leading these developments?
Q.9 Who are the major players in this market? What strategic initiatives are being implemented by key players for business growth?
Q.10 What are some of the competitive products and processes in this area and how big of a threat do they pose for loss of market share via material or product substitution?
Q.11 What M & A activities have taken place in the last 5 years in this market?